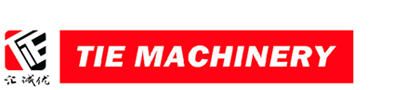
Power cables of 35kV and below |
Publisher:admin Click:564 |
In recent years, many enterprises in the wire and cable manufacturing industry in China have made technological innovation and progress in optimizing product structure, adopting new processes and applying new materials for power cables with voltage levels of 35kV and below in order to adapt to market competition and avoid homogeneous vicious competition, and control manufacturing costs on the premise of ensuring quality. Specific aspects are as follows: ① Product structure. Medium voltage power cable is transiting from round compact conductor to stranded conductor. On the basis of ensuring that the DC resistance of the conductor conforms to the provisions of the standard, the outer diameter of the conductor is reduced, the material is saved, and the conductivity of the copper conductor is improved; The conductors of low-voltage power cables with large specifications are transited from compact sector structure to non compact strand structure, so as to make full use of the conductivity of the single conductor wire and avoid the decline of the conductivity of the single conductor wire due to compact deformation; The inner liner of armored power cable is changed from wrapping structure to extruding structure, which makes its overall performance better. ② New process. For the conductor manufacturing of medium and low voltage power cables, most enterprises in the industry generally adopt the copper wire drawing annealing integrated equipment process, frame stranding and high-efficiency stranding equipment process. The new UV crosslinking process is being popularized in low-voltage cable production to remove the warm water crosslinking process necessary for silane crosslinking process and shorten the production cycle. For silane crosslinking process, "one-step" crosslinking process has also been rapidly promoted in recent years. ③ Application of new materials. UV light cross-linked insulating materials are emerging for low-voltage cables; In order to meet the environmental requirements under combustion conditions, low smoke and halogen-free sheathing materials have been widely used, especially in the past two years, low smoke and halogen-free sheathing materials that meet the requirements of the GB 31247 standard with Class B1 combustion characteristics have been developed and applied; In order to improve the environment and make waste cables recyclable, enterprises in the industry have cooperated with universities and scientific research institutions to promote the application of thermoplastic PP materials in the insulation of medium voltage power cables as a supplement to the XLPE materials widely used at present. Although there is a large market demand for medium and low voltage power cables, there are many manufacturers, with low barriers to technology and equipment entry, low technical barriers, serious homogenization, overcapacity, aging equipment, low equipment control accuracy, unstable material performance, and many by-products in the cross-linking process. In addition, many enterprises have insufficient management and innovation capabilities, resulting in vicious competition in the market for products, and the quality is not guaranteed by competing for orders, Cable failures and quality problems often occur in major projects. These problems include that the DC resistance value of cable conductor exceeds the standard, the insulation thermal extension and insulation shrinkage are unstable and not up to the standard, and the indexes such as flame retardancy, light transmittance and sheath thermal weightlessness do not meet the standard requirements. |
Prev:Analysis of offshore wind power and submarine cable industry Next:Current Situation and Development Analysis of Power Cable and Accessories |
Scan QR code